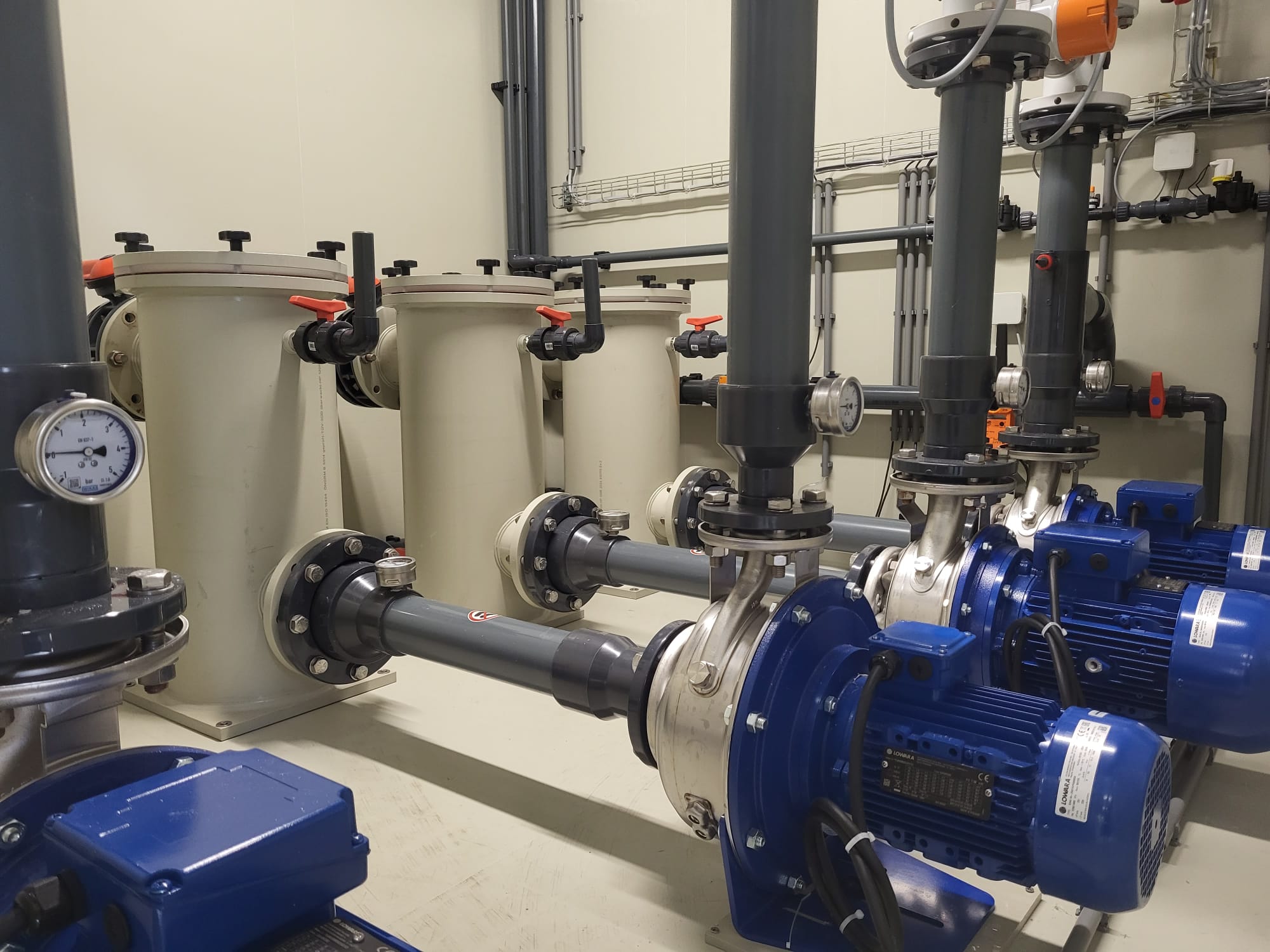
InnoHeat
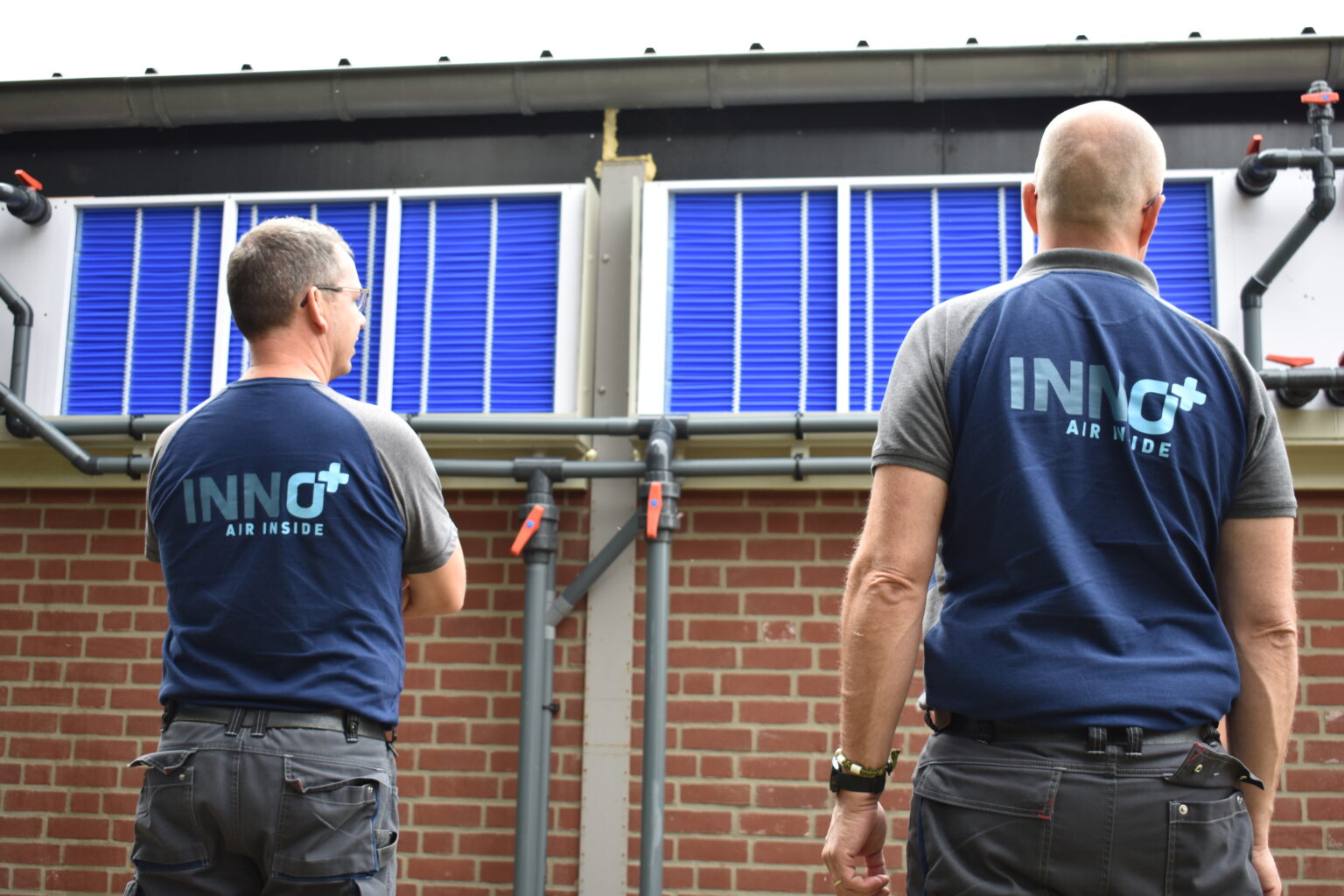
How does it work?
Approximately 60% of the feed given to animals is converted into heat. InnoHeat utilises this natural heat by transporting the heated process water from the air scrubber to a heat exchanger. The heat in the water is then transferred to the supply circuit of the barn’s heating system.
Applications
- Preheating incoming air: Heat can be used to preheat the air entering the barn via heat exchangers in the air inlet.
- Heat pump support: The heat can also serve as an input for a heat pump, assisting in heating the space itself.
- Combination of both: Both methods can be combined for even more efficient use of available heat.
Benefits for your business
- Optimal barn conditions: By maintaining a constant, comfortable climate free of cold draughts or moisture, animal welfare is improved, positively impacting their health and performance.
- Energy savings: InnoHeat can save up to 90% on heating costs by utilising available heat.
- Low energy costs: Efficient heat use and low energy costs make InnoHeat a highly cost-effective choice for any livestock farmer.
With InnoHeat, you create a win-win situation: providing your animals with a healthy, optimal climate while significantly reducing your energy costs.
With Synergy+, optimal barn conditions 365 days a year
By combining InnoClean, InnoHeat and InnoCool, you are guaranteed a constant climate, 365 days a year. This integrated approach ensures optimal barn conditions, allowing your animals to perform under the best conditions. Smart cooperation between all systems helps you save substantially on energy costs. Heat exchangers in the air intake system provide heating in winter and cooling in summer. The air scrubber efficiently recovers heat from the stall air, allowing you to create an ideal climate at the lowest cost. Vital and healthy animals perform better, which benefits not only your bottom line, but also your job satisfaction.
- InnoClean – Reduces emissions and improves air quality.
- InnoHeat – Uses heat recovery systems to reuse energy, reducing your energy costs.
- InnoCool – Controls the temperature in the barn, prevents heat stress and improves the productivity of your animals.
Together, these systems provide the ultimate balance between energy efficiency, animal welfare and environmental responsibility. Synergy at all levels!
Eliminating outside stress influences
Minimizing inconvenience to the environment
Maximizing energy recovery
Payback period of up to 5 years
The application of our InnoClean air scrubbers, combined with InnoHeat
and InnoCool, offers a solution for emission reduction, energy savings and an optimal barn climate. With this Synergy+ approach, we realize a payback period of up to 5 years thanks to:
- 365 days a year optimal barn conditions
- Improved animal health and productivity
- Lower production costs
- Saving energy costs through heat recovery
- Minimal emissions
For more details and success stories from our customers, download our case studies.
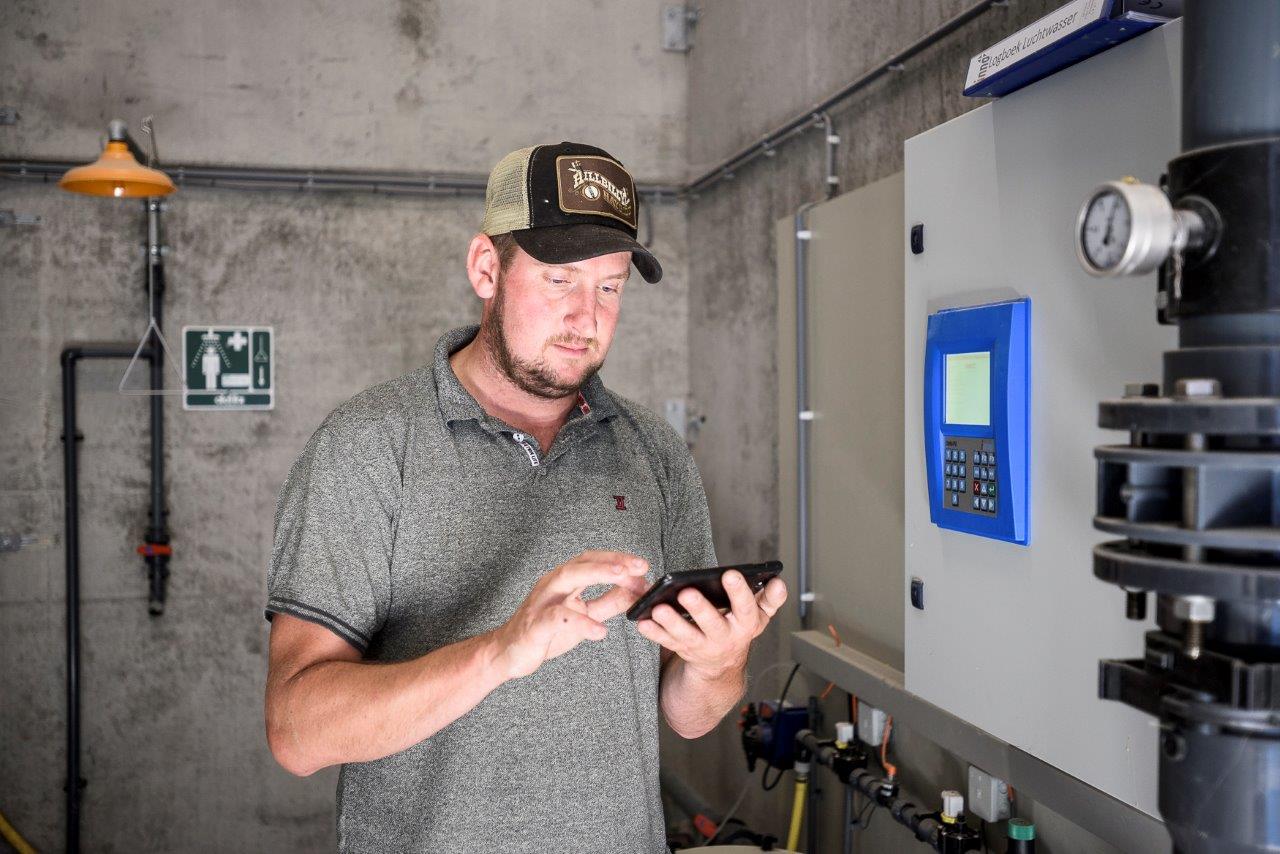
We energise farming
Want to know how much you can earn with our Synergy+ technology?

Pig farming
Provides a stable environment for piglets and finishing pigs, promoting their growth and health.
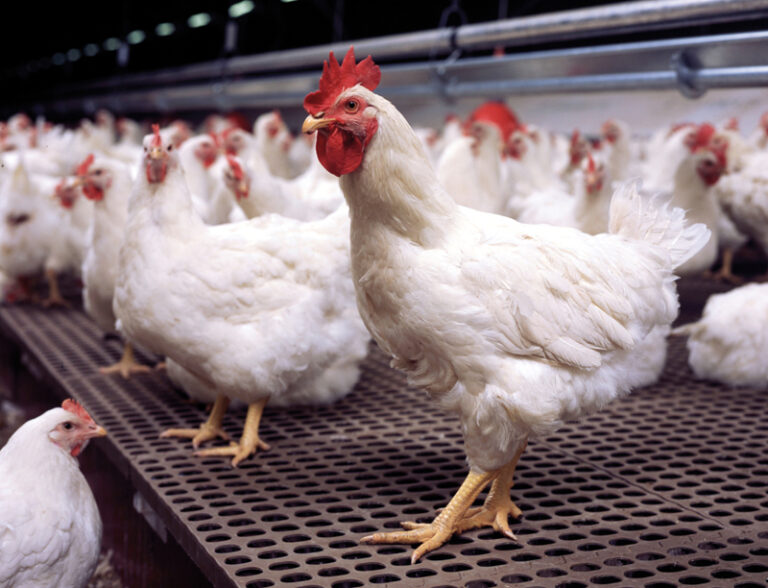
Poultry farming
Keeps the temperature stable and lowers energy costs while optimizing the well-being of your animals.
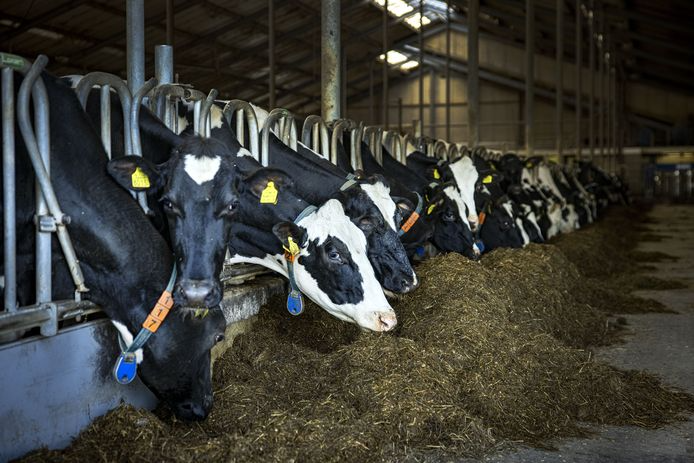
Cattle farming
Creates a constant barn climate that leads to higher productivity and better health of your livestock.