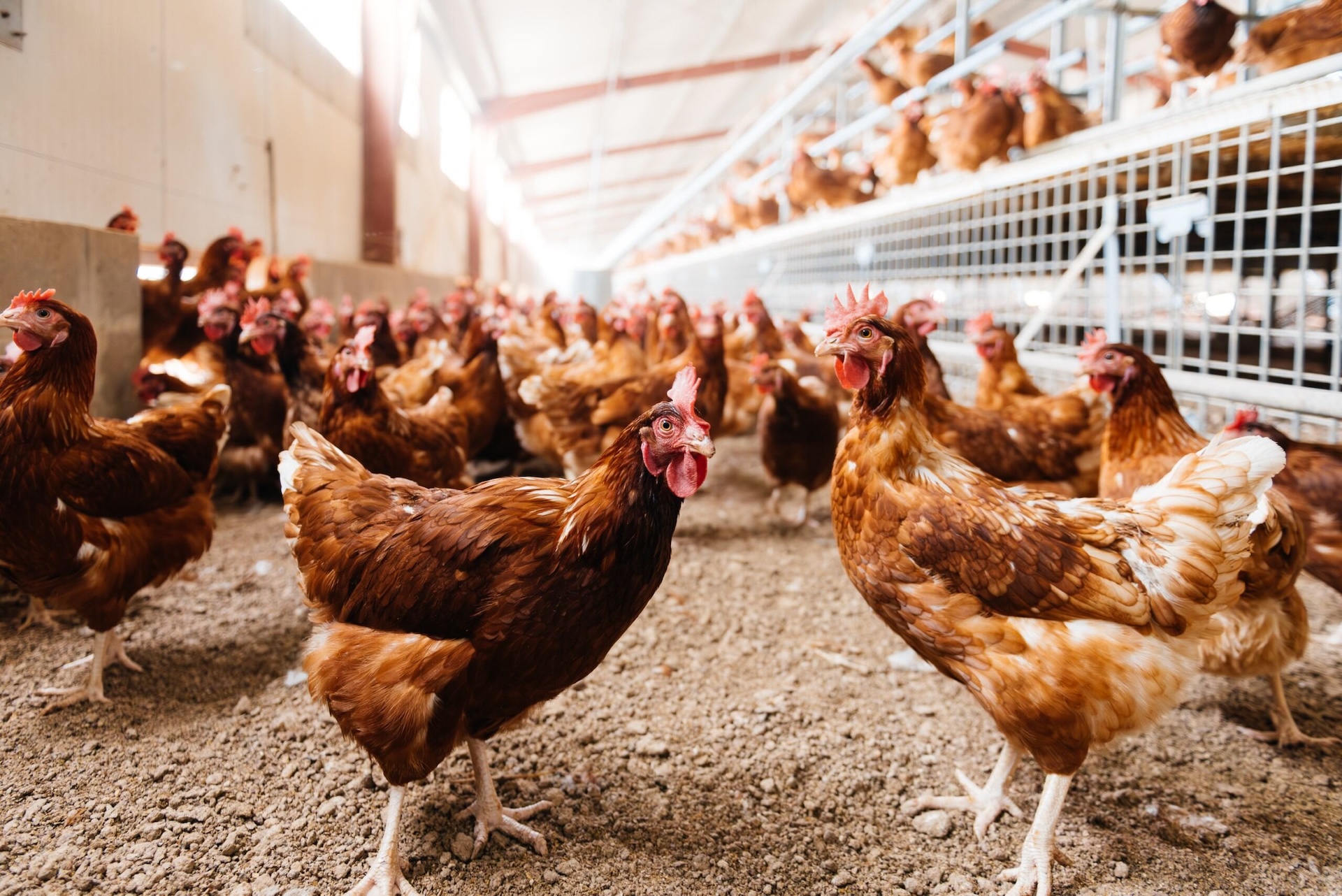
Knowledge base
Our knowledge base provides you with the latest news on projects, product developments and sector-related updates. We share insights on innovations within Inno+, developments in animal husbandry and manure processing, and new applications of our solutions. Stay up-to-date on trends and technologies that we use to contribute to a sustainable and efficient future for your business.
We energise farming
Want to know how much you can earn with our Synergy+ technology?